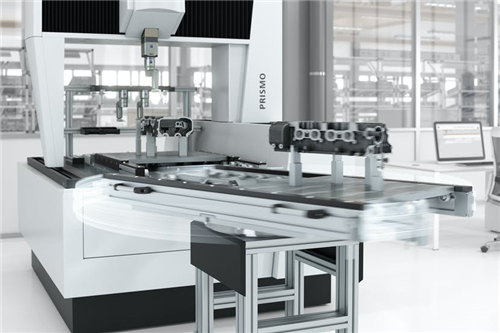
早在1967年,通用汽車就開始采用工業(yè)焊接機(jī)器人。寶馬美國斯帕坦堡工廠則在全球范圍內(nèi)率先在系列化生產(chǎn)中成功采用協(xié)作機(jī)器人,為BMW X3的車門精密、高效安裝隔音防潮件。
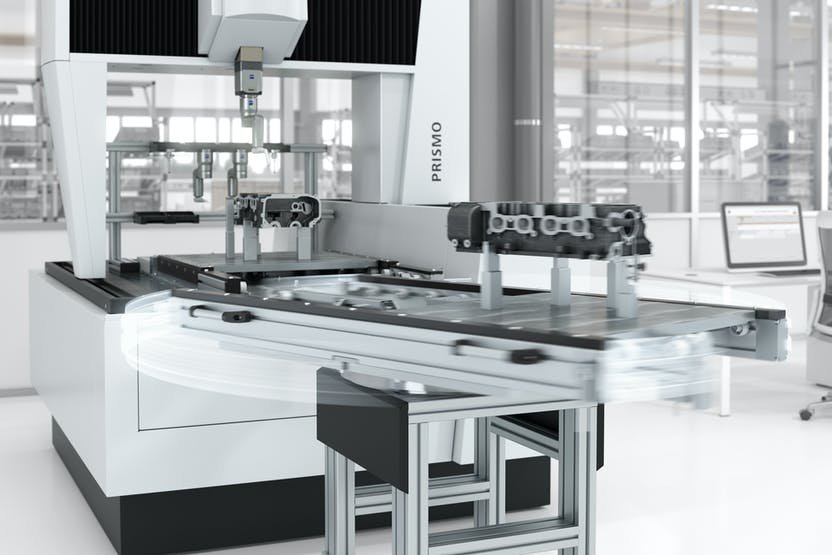
蔡司三坐標(biāo)對自動化智能工廠投資不斷增長
對100家年收入超過10億美元的全球主要汽車OEM的調(diào)查顯示,過去三年中,約有30%的OEM對工廠實(shí)現(xiàn)了一定程度的智能化,未來五年,這些企業(yè)44%的工廠將被改造成智能工廠。梅賽德斯-奔馳已經(jīng)利用虛擬工具模擬整個生產(chǎn)過程,并用先進(jìn)的數(shù)據(jù)分析創(chuàng)建自我學(xué)習(xí)和自我優(yōu)化的生產(chǎn)系統(tǒng);雷諾通過部署協(xié)作機(jī)器人、AG和增強(qiáng)技術(shù),每4秒可生產(chǎn)一輛新車;奧迪墨西哥智能化工廠有望提高效益30%
華晨寶馬鐵西工廠擁有現(xiàn)代化汽車制造的完整工藝:沖壓、車身、涂裝及總裝四大車間,生產(chǎn)七款寶馬車型。其中,車身車間擁有超過600臺機(jī)器人,自動化率達(dá)到95%以上。相關(guān)數(shù)據(jù)顯示,通過全面實(shí)時工業(yè)智能化,機(jī)器人熱能回收技術(shù)每年節(jié)約超780萬度電,在汽車制造耗能的涂裝環(huán)節(jié)(約占汽車制造能耗的70%),實(shí)現(xiàn)節(jié)水30%、節(jié)能40%、減排20%。相比傳統(tǒng)液壓機(jī),其高速沖壓機(jī)生產(chǎn)效率超過70%,節(jié)能50%。
蔡司三坐標(biāo)在線自動化解決方案
蔡司在線三坐標(biāo)測量技術(shù)可以在在初始工藝進(jìn)行錯誤檢測,從而避免高昂的大量后續(xù)返修及高附加值損失
蔡司三坐標(biāo)測量機(jī)為自動化技術(shù)順利實(shí)施提供全面測量與檢測支持
蔡司三坐標(biāo)可滿足從單個部件到全球產(chǎn)業(yè)鏈,從傳統(tǒng)汽車到新能源汽車的各種需求。